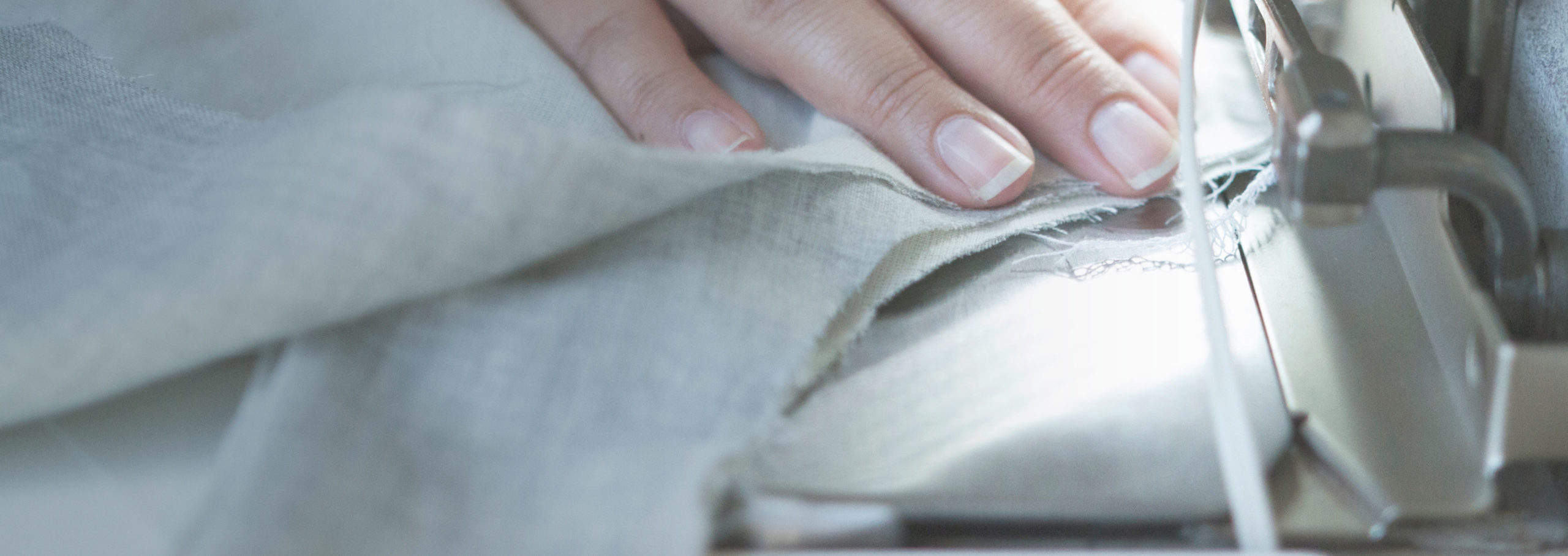
Have you ever wondered what it’s like to work in the fashion industry. To make it as an artist, the hustle behind launching your own label, pursuing a career in music or any other creative industry? Halfstack has been pursuing these stories in print form for the last four years. This fall, we’re bringing the insight story to YouTube. We connected with some of Chicago’s most iconic creatives to hear their stories and share their journeys with you. We take you behind the scenes and offer candid, personal conversations with people pursuing their dreams. It’s not as glamorous as the media would like you to think. We are sharing the raw reality behind making it.
In this episode of making it, we’re introducing you to The Apparel Agency. The Apparel Agency is a full service development and production management agency. They worked to bring success to apparel brands for worldwide through their comprehensive plans in private labeling, located in the heart of America’s Midwest. The Apparel Agency is based in Chicago and has a fully equipped team of industry professionals, creative and technical designers. Pattern makers, sample makers and access to production facilities to aid in the development and the manufacturing of apparel accessories, and so much more. We visited The Apparel Agency over the span of a few months to learn more about the process behind launching a clothing label. They let us get a behind the scenes glimpse of what they worked through with clients.
In this episode of making it, we talked with The Apparel Agency’s, production team about the production process and all of the steps necessary to prep a line for manufacturing. This is the final step in The Apparel Agency’s client process. We learn about how a product goes from idea to pattern, to sample, and then into production run.
The team gives us some insight on how they take raw materials and transform them, all the while keeping in mind production volumes, the needs of their manufacturing partners, and their clients supply chain. If you haven’t already, please let us know if you’re enjoying the series, give us a thumbs up or subscribe to keep up with the newest episodes of making it.
Can You Tell Us What The Build Process Entails For Clients?
All of our build phases around our technical department, so everything will be the tech packs, patterns, and getting that first prototype cut and sewn so that we can test all of the fit and function of the garments.
What Are Some Of The Key Steps Involved In The Build Function & Process?
It starts out by our designer handing off the finished design specs to our technical team. And so from that point, the technical team gets all the information they need around the aesthetic and the way the garment should fit, and then they take the ball and they start developing the patterns size specs, finishing it, and routing out the garment. From that point, the next step really is taking it to make a sample, and then we go into fitting stage where the customer gets to see the garment for the first time made into a sample.
What Team Roles Are Involved In This Phase?
We have an office, the pattern maker, and then we have our technical designers who will do the tech packs and all the specs and sizing specs, etc. And then we have our sample sewer who’s in office as well. And they’ll do the cutting and sewing of those prototypes.
Do You Use Any Special Type Of Software During Tech Design Work?
The main piece of software that we use that isn’t generally something everybody uses is Optitex. It’s a software specifically for the apparel industry for making the patterns, marking, grading, and it’s kind of expensive piece of software. So it’s not something that everybody will have at their home doing it themselves. So that’s the main thing that sets us apart. And then we have our own plotters so we can print patterns in house, which is very useful. All the production markers and everything that you need to kind of prepare to send off for cutting. We can do all of that in office instead of having to farm that around to printers and things like that. Then all of our tech packs and things like that, we use Excel or Adobe illustrator. So typically those are a little more typical programs.
What Are The Final Steps In The Process Before The Product Hits The Factory?
The key things we’re looking at is when we have the first fit sample, we meet with the clients and we get their feedback. So the most important thing is that they like the way it looks on a model, it fits well, and it functions the way they expect it to function, if there’s a specific functionality to this garment. After those are all approved, then it gets approval for going to production.
Great cut tickets. We’ll lay out the markers for whatever the production order is, whether it’s samples through a full production run. And then we bundle up anything material-wise components for the garments, and then that’s kind of what we send off for the product.
Do The Factories That You Work With Require Any Minimum Orders?
It depends. We work anywhere from small batch manufacturing, sample making, and then we can scale up to import manufacturing, where they do have slightly larger minimums. We’re really set up to meet the needs of the client. So anywhere from small sample making up to somewhere in the couple of thousands. We can do pretty much that and everything in between.
How Do You Balance Factory Needs Vs. The Needs Of Your Clients?
So definitely working with the clients on the minimums, what’s going to get them best pricing because a lot of times they want to keep it smaller, but we can have a little bit of wiggle room to be able to work with our factory and have a better order for them. And then whether we’re bringing that down to different color ways or making it a little easier on the clients, they can have some different skews. We can definitely do things like that. The contractors that we work with really enjoy working with us. We’ll go back and forth if it doesn’t really work well to kind of meet the needs of the startup type clients, so that we can keep going and keep getting those orders back and forth for each season.
We really built a network of contractors and larger factories that are willing to work with many different types of clients. It’s very tailored. Our, our factory base is very tailored for this type of business. So they kind of rely on our repeat business.
Do You Work With Only Local Or Do You Also Have Ties To International Factories?
We’re tied with factories all over the world. So we do a great deal of our manufacturing in Chicago. We also partner with a few on the west and east coast, but then for larger clients or specific orders that make the most sense to do import, we also do work with factories that we partner with anywhere from India, Cambodia, Vietnam, China, Morocco, Italy. So we have a pretty wide network.
What Is The Biggest Obstacle That A Brand Might Face During Production?
A lot of it is pre-production, a lot of it’s costing, figuring out the timing of your production. And that’s where we come in and we try to help bring everything together and make it a little more seamless for them, but during production, the biggest thing really comes to just managing the time and trying to make sure that everything comes together and then gets delivered on time.
What Other Services Do You Offer After Production?
We actually do like pick and packing or fulfillment of their orders. We have Apparel Magic, its one of the programs that we use and we can sync up different Shopify accounts or websites that they can sell it, and we’ll actually send the order directly to us and we can ship it out from our warehousing. That way they don’t have to store everything. If they can’t get into a regional distribution centre because they don’t have the amount of units that are required. We can still offer that and that same pricing, but at a lower quantities.
Follow us on Instagram @theapparelagency!
Original video & interview by The Freelance Life
Link: Meet The Apparel Agency – Making it – Episode 3: The Build Process At The Apparel Agency